We were curious
In our last post, “A different kind of light”, we told you about our experience buying, assembling, and installing a unique light fixture for our dining room.
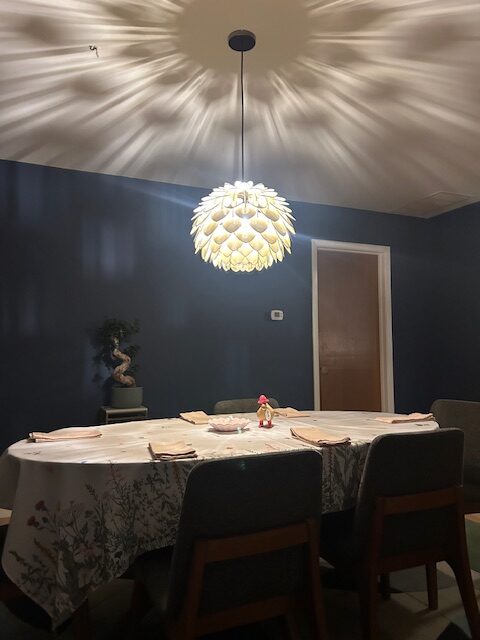
We bought the lamp from Vien Nguyen, an artisan in Vietnam who runs a shop called Enlightening Decor on Etsy.com.
As we wrote in the post, the entire experience of interacting with Vien was excellent and we wanted to know more about her, her products, and her business. So Mary sent her some questions and asked if she would tell her story so we could share it here. Vien agreed and so today, we’re delighted to give her space to tell you about herself and her business.
Note: We added the images in the section below.
A note from Vien
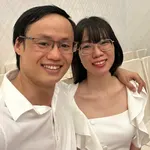
Dear Mike and Mary,
How are you?
I have prepared my answers. And here they are.
1. Tell us a little about your background. Where did you grow up? 2. How did you get interested in starting a business? What challenges have you faced in growing your business and making it successful?
My name is Vien. I am the face behind the Enlightening Décor. I am 35 years old. I am Vietnamese. My hometown is Danang city, which has the most beautiful beaches on Earth. I lived and went to college in the States for 5 years from 2008-2013. There were times when I felt invincible with what I was able to accomplish during my study in the States. But life hit me hard and I am back to 0 when I was home in 2013.
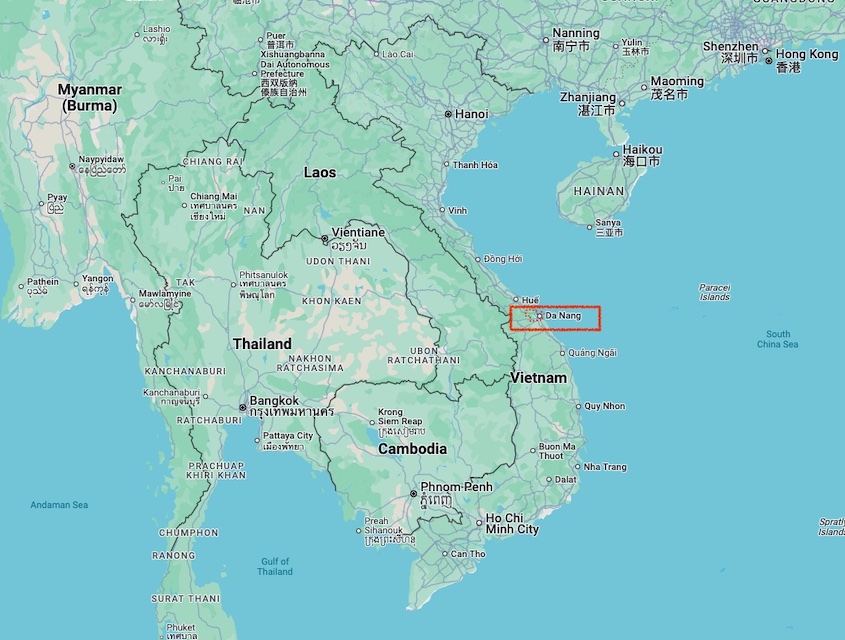
I was miserable, bitter, painful, hopeless and heavily depressed. Eventually, I took steps to help myself. During this time, I learned about the power of the brain, the mind and meditation. My healing began and I was able to get back to normal life in a year with my daily meditation. When I meditated, personal distress, emotional scars, sufferings and painful memories were slowly taken off of me. I fell in love with life again. More than that, I wanted to grow, thrive, prosper, help, love, give and make a positive impact.
At that time, I was working for a large telecom company in my town and it was a job that I didn’t love. I did meaningless work for little money. Although I wasn’t sure what it was in life for me, I was certain I was capable of being more. While having my day job, I ventured into different businesses and took many online courses at night. I did everything from drop-shipping to bulk purchasing and selling things on eBay. I had some small success, however I always felt something was missing. I sold so many products and it was just merely focused on how much money I can make.
I remembered one day while searching for a product to source and sell on eBay, I stumbled across a wooden desk lamp and it was an enlightening moment! I have always loved creative handmade lights made from wood. Lights given off from the wooden lamp can speak to my soul at a deeper level. Its lights can elevate positive energy, evoke warm cozy feelings, recall fun old past memories and love inside me.
I started searching, sourcing and testing so many wood lamps myself. I found all around the corners in the locals, Etsy and other marketplaces. Talking about the material and craftsmanship, I can only find two types of wood lamps: (1) natural wood lamps that are either untreated, or treated insufficiently (i.e not going through a proper wood treatment process for wood protection and custom stain color, beautiful finish); and (2) MDF wood lamps (laminated manufacturing wood with already made colors to choose from). Both options are cheap, easy and simple to make. Basically, once we have a design, we can just machine-cut it and ship it. That is it!
But I saw there was a huge gap from where it was to where perfect quality and superior finish appearance lies. I figured out there are so many things that can be improved, from the material, the assembling experience, the designs, and most importantly the quality and lifespan of these wood lamps.
How is the Enlightening Decor different? I create beautiful wood lamps around flowers made from natural wood and turn them into perfect interior wood design items that are top notched Polyurethane (PU) wood treated, as perfect as your hardwood floor, dining table or kitchen cabinet! I chose the more difficult path! It is harder to make, and requires an extensive amount of labor and care to give these tiny wood pieces their PU coatings, not just on one side but both sides, plus all edges are protected! Polyurethane requires 4 to 5 coats depending on the color stain, times two sides of a wood piece would equal 8-10 coats for a lamp. And I stain every single piece of the lamp all by itself, and not put them together and stain the whole lamp. Why you might ask? Because doing PU coats to the pieces separately gives a more even, thorough application, better protection for the edges and more beautiful result!
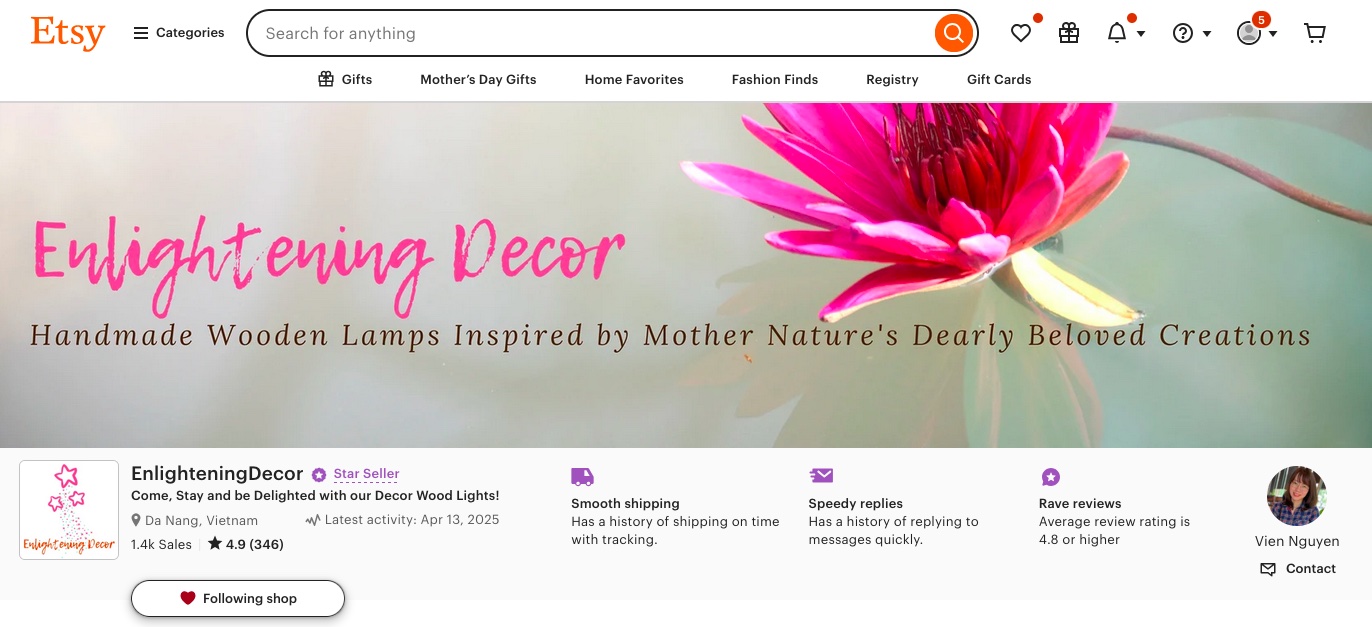
I have had my customers who opened the box and could appreciate the finish of the wood right away. Although it is much harder to carry out than simply cut and ship, I take my pride in making beautiful and meaningful lamps that are of top notch quality.
From only me carrying out all tasks back when I first started, the shop has now grown to 5 members – me and my husband, my cousin, and two young professional painters. I didn’t know how we managed to arrive where we are today. Without your support, I couldn’t have made it. And with the customers’ great reviews, the kind and encouraging words and all the constructive feedback for me and my work are the things that helped me keep going despite endless obstacles and challenges.
The biggest challenge for me has been the Polyurethane wood treatment part of the craft. It requires the painters to be very meticulous with their work with extreme attention to detail, and have great skills of course. Most painters have little experience working with the material I am working with (natural wood pine and birch plywood) because they mostly work with natural solid wood in furniture. It is much easier to work with large surface wood like furniture than hundreds of tiny little pieces of wood that are very light in a lamp. And like I said, I do PU coatings for both sides and edges for 100% protection and beautiful finish.
So for them and for us, we had to start from zero. We had to experiment, test, observe, and learn. Fix, retest, observe and learn. Gradually we developed a formula to work with the material. Not only did it take time, it was a very expensive process, especially for a small business. The thing with this trade was, once a batch was failed (i.e the finish result did not come out as expected, with errors, even the smallest errors), I would be better off starting a new batch and redoing it all again rather than fixing the old batch because it would be more costly to fix it than to start from scratch. There is something about this material that the more you fix it, the worse it will become. Either redo or fix, you would be mostly at a loss because cost of material, cost of PU supplies, and cost of labor are expensive.
Highest of all is the cost of labor. Staining on both sides makes it harder to achieve a beautiful flawless finish. Oftentimes, the first side is easier to achieve however, the other layer is much harder to carry out and it will cause errors on the first side. This has to do with the chemical reactions when you do the second side, residue gas products from the spray painting will be printed onto the first side, which was beautiful and now failed.
Some other challenges that I faced are the workplace and the weather. In my first two years, I used to do my crafts in an abandoned park near my house. To do PU, it requires clean and large areas for the work. However, when the weather is unfavorable (windy, rainy, or too hot) we have no way to but to stop the crafts. If I had orders during that time, I would have to find ways to speed up the process, and it was really a mess because if I took a step in a hurry, I might have to redo the lamp from the start.
At first it was OK because I only had a few orders a week and I could work around it. Gradually, I rented another place to put my shop in the front and built a small house in the backyard for PU work. We have been in this place for 2 years now. Since the place is quite small and there are houses in the surrounding area, we can only make about 30-40 lamps a month at the moment. And I am now averaging about 30-33 lamps a month on Etsy. I couldn’t board more painters nor work outside regular work hours or on weekends or holidays because I can’t bother my neighbors.
It will be easier if I can sell more of my lamps. I will be able to move to a permanent, larger workplace for us and the staining activities. We can expand and grow without restrictions and I can just focus on bringing my lamps to more customers. There is this transition time, where I need to grow my shop first, do more marketing and develop more products for the shop to get to 100 lamps a month. And if I can make it, I will be so busy arranging one more small workplace to work in parallel with the current one. It will be fun and crazy too but I am looking forward to it:)
3. Can you tell us something about how you design and manufacture your lamps? (My husband is very interested in knowing how you create the very precise parts that make up the lamps.)
It is quite a simple process after you have seen thousands of lamps. You got the ideas how it works, the basic structure! My inspirations for my lamps are beautiful flowers from nature. Once I have a design idea in my mind, I would sketch the flower on paper. Once I can feel the flower, I would sketch the petals and have my husband build the design files of the pieces using CorelDraw. There are only 5 basic details of a lamp, that is the top and bottom circles, the two types of sticks where the petals will go in along these sticks, and a petal for the main shape, other petals will be variations of the main petals. CorelDraw makes it easy to work and adjust the shape of an item. I would then test-cut the pieces and make any adjustments accordingly.
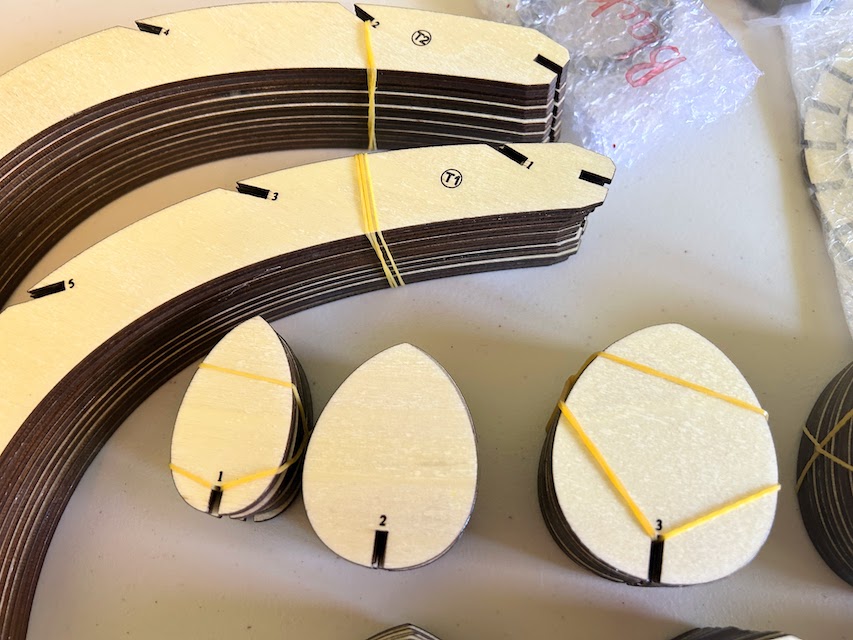
Having a laser machine allows me to experiment with the designs freely and be the most creative that I can during the process. I would build many draft lamps and see if the results match my imaginations. I would see and make changes to the shapes, shapes of the petals, shapes of the frame, the angles where the petals go, the proportion of the petals to the flower center, adding or cutting layers, adjusting the distances between the layers, and whether it looks like a real flower in real life or not. I would then ask for feedback from my team. Once I am happy with a design, I will install the lamp on the ceiling to see how the lights and patterns it gives on the ceiling. I might add more details to parts of the lamp to increase lights/shadows on the ceiling.
Now to the manufacturing process of the lamps. My lamps are made from 3mm and 5mm natural wood plywood (pine and birch wood). My husband will measure how large each slot needs to be so that customers can assemble the lamps quick and easy, and most importantly no glue is required. After receiving some feedback about the hassles of wood glue from my past customers, I made changes to improve the assembling experience for my future customers. I can’t include glue in my packages because it is a liquid. Some drawbacks of using wood glue are, it adds more costs for the customers, extra work to apply glue when assembling, customers might choose wrong glue, the glue might damage the finish of the lamp and create a mess, and finally glue makes it hard to uninstall parts and clean the light when needed.
The thickness of the plywood in one batch can vary ±0.2mm, and the cutting from the laser work can vary ±0.1mm. And I need to make sure after applying 4-5 PU coats, they fit together perfectly. Therefore, each lamp has to be calculated very carefully before cutting and no mistakes are allowed because once it is stained, there is no way we can adjust the slots. Design files are adjusted each time a lamp is cut to ensure a perfect assembling experience for the customers. This alone is easier said than done.
Before having my own machine, I used to outsource this task to laser machine cutting services. They couldn’t be as detailed as us doing for ourselves, making perfect assembling experiences very hard to accomplish. Some lamps will be tight, which requires extra manual work to enlarge the slots by hands before they can be stained. Or some lamps will be a bit loose, which will require glue for security. I would inform my customers about the required glue beforehand and ask them to help get the glue from online or from local stores. Most of my customers are so nice and kind and would help with getting the glue themselves! Later, I was able to improve this aspect of the assembling experience for my customers! I received better satisfaction and greater feedback on the simple, quick, and fun assembling experience too.
Once a lamp is cut, I will give them to my two painters. The lamp will go through a series of steps for a total of 4-5 PU coatings, including applying sealer coats, sanding after each coat, reapply, sand, reapply, sand, color stain coat, final finish coat. Each step will be 6 hours-24 hours apart.
Once the staining is finished, the lamp will be quality checked for any errors, piece by piece. I always stain extra to make sure a lamp will be complete with all the parts after passing the quality check. Once quantity and quality check is done, the lamp will be placed in a dry, clean, well ventilated area for the chemical smells to dissipate. I let them sit for 48 hours at least before packaging them.
4. What are your plans for the future? Do you plan to expand your product lines?
I am working on my own website besides Etsy. I want to bring my lamps to more customers and I am thinking of promoting my online store on social media. I am going to focus on Pinterest first.
For now, I would like to focus on my flower lamps. In fact I have already created more flower designs and I am looking to add them to my shop soon.
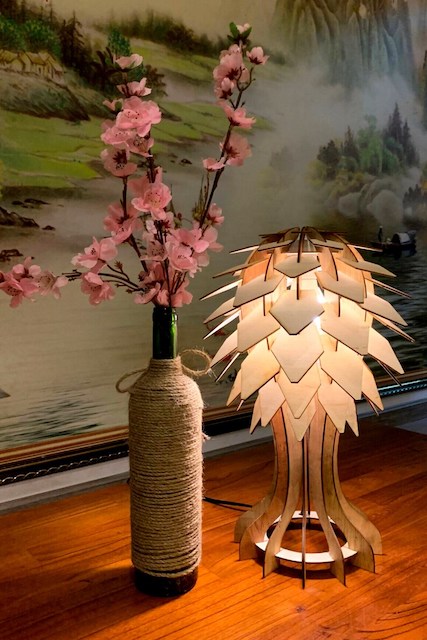
I hope that I will sell more lamps in the coming time, I am looking at 60-100 lamps a month, and I will be able to move our shop to a better working place, where we can work on our own terms and I won’t have to worry about our work bothering any neighbors, or having sleepless nights during time of unfavorable weather conditions.
5. Anything else you’d like to tell us.
For a long time, I have always wanted to humbly change the world by doing meaningful work that I love. I guess I made it! Finally, with my wooden flower lamps, I hope to bring you love, to spark and inspire positive lights into your life. Thank you!
Please feel free to let me know if you have any other questions or concerns. Thank you very much for your generous help with bringing my lamps to your readers and followers. I am very thankful! I wish you both all the best of the best!
With Love and Gratitude,
-Vien
Concluding thoughts
Here in the US, we have traditionally celebrated the “Horatio Alger hero” – the young person who rises beyond their starting point “to achieve financial security and success by overcoming obstacles through hard work, learning, solid morals, and a little help from others.” We found those same attributes in Vien’s story. Learning more about her gives us a greater appreciation for the lamp that hangs in our home.
This post probably sounds like an extended advertisement for Enlightening Decor, and to a certain extent it is. But we will not receive any compensation from Vien. This is simply our way of celebrating a determined, innovative young woman, helping her reach a broader audience, and maybe encouraging others to follow their dreams.
Until next time,
Mary and Mike
The Cook and The Writer

What’s the story behind one of your favorite things? Tell us your tale in the comments below or via the Contact Us form.
I enjoyed reading about Vien’s personal journey and the dedication to her craft. Wonderful, too, that you’ve given her a forum to share her story and expertise to a larger audience. <3
I can vouch for the beautiful beaches adjacent to DaNang Bay. I flew over them in 1968 when Vietnam was a different place 55 years ago.
I am amazed by the perseverance mustered up by those who endure the harshness that greets so many each day.
May graceful spirits watch over them.
Truly a wonderful story and jogs my memory of just how resourceful the people from Southeast Asia really are. Most are wonderful, caring people. My year stationed in Thailand during the “conflict” taught me a great deal. She sounds like a wonderful person.
What a wonderful story Vien’s is! I have read and reread the interview you published, and I must recognize that she’s a special person. Vien deserves so much success for the care with which she makes her products, for the modesty and depth of her soul. I would love to have the opportunity to meet her.